How can a global leader in industrial solutions recover when they realize their supply chain is more fragmented than connected? How does a company with a vast network ensure seamless planning and forecasting across continents? SKF, a 9 billion industrial manufacturer, confronted these challenges by transforming its supply chain planning into a harmonized way of working.
CHALLENGE
A supply chain ready for transformation
For years, SKF managed its supply chain regionally, with operations spanning over 94 manufacturing plants in 24 countries, serving more than 130 markets with a wide range of products. This decentralized approach made it difficult to gain a clear, company-wide picture, impacting agility and decision-making. As the company grew, so did the need for a global, streamlined approach to supply chain planning. It was time for a change.
SOLUTION
A strategic shift to global planning
SKF’s supply chain was too scattered—each region had its own way of forecasting and planning, making it nearly impossible to get a clear, company-wide picture. To stay ahead in a competitive market, they needed a more connected approach.
That’s when they decided to team up with Optilon. Together, they introduced a powerful solution designed to harmonize planning, optimize inventory, and automate key processes. The journey was mapped out in four key phases: feasibility, proof of concept, pilot, and deployment. Step by step, SKF moved from a fragmented system to a seamless, data-driven approach. It was a full-scale transformation.
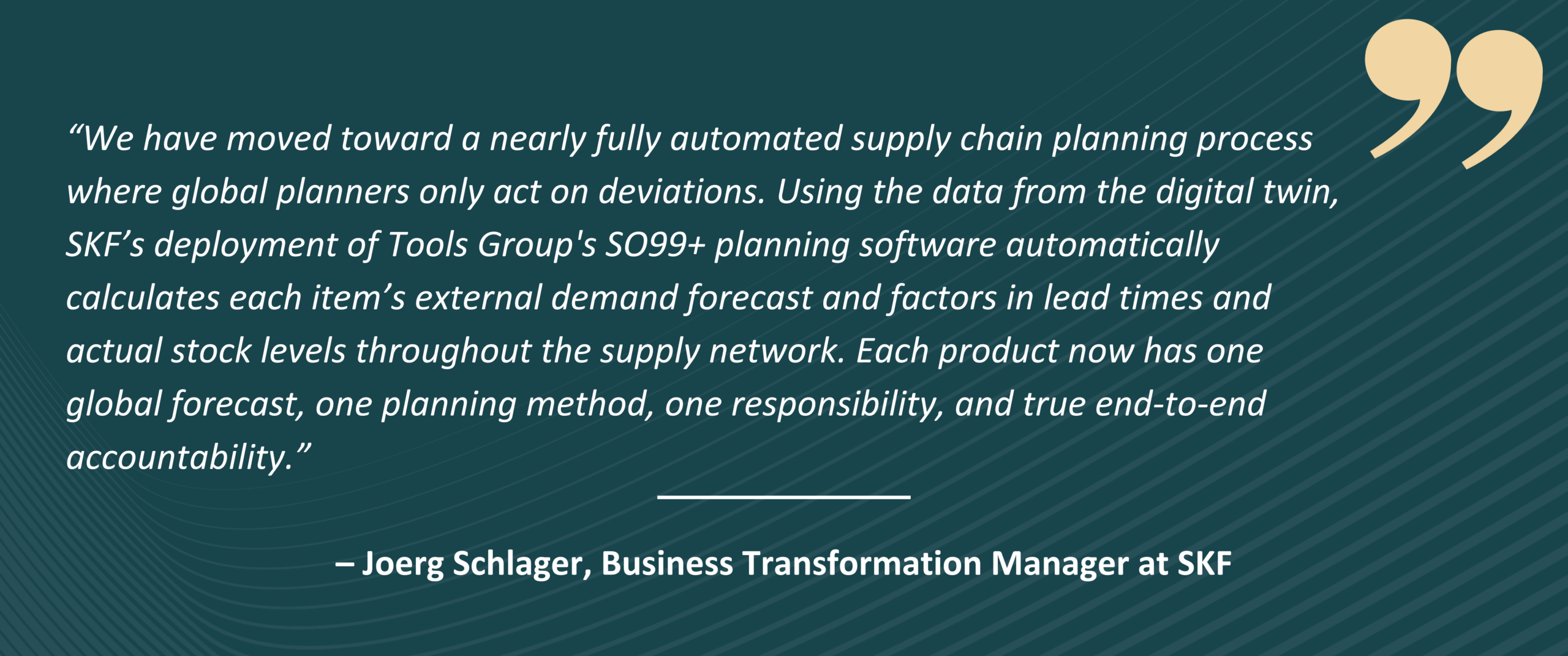
RESULT
Results and benefits of Optilon’s planning solution
As with any major transformation, it took time for SKF to adapt to a new way of working. Ensuring planners were on board and engaged in the process was key to building confidence in the system. But once the team embraced the changes, the benefits quickly became clear:
MAIN BENEFITS
- Reduced manual work by 20%, enabling a nearly fully automated supply chain planning process.
- Improved demand forecasting accuracy by leveraging digital twin data and automation.
- 14% reduction in inventory achieved through optimized inventory management, advanced safety stock calculations, and replenishment planning—while maintaining service performance.
- Increased responsiveness to market changes through real-time deviation alerts.
By embracing automation and intelligent planning through its partnership with Optilon, SKF transformed a scattered, manual supply chain into a streamlined, highly responsive operation. With better forecasting, clearer decision-making, and a more connected planning process, SKF is now equipped to handle challenges, drive efficiency, and stay ahead in the global market.
About SKF
SKF is the world’s largest bearing producer, serving 130+ countries and 40 industries. With 94 plants in 24 countries, SKF is automating Supply Chain Planning, allowing planners to focus only on deviations.
In 2020, SKF received the Gartner Supply Chainnovator Award in the industrial category for its innovative use of a Digital Twin, implemented in collaboration with Optilon using the Optilon Integration Platform (OIP). Gartner describes the award as part of an annual program that “identifies, assesses, and awards outstanding examples of supply chain innovation.” The initiative recognizes unconventional, high-impact projects that are transforming supply chains and setting new industry standards.
Struggling with supply chain complexity? Let’s talk.
With a track record of over 1,000 successfully completed projects and 20+ years’ experience, Optilon is your trusted supply chain optimization partner. Book a meeting with us to discuss how we can help you create a solution that aligns with your specific needs and future business goals.