ABC inventory classification has been around for so long that most planners just assume it is the only way to segment inventory. Spoiler alert: it is not. And it is far from the best way. This method hails from the 1960s, a time when computers were room-sized giants. Today’s tech can do so much more. Let us dive into how inventory management has evolved into multi-echelon inventory optimization (MEIO), helping companies minimize inventory investment while hitting service-level targets and improving profitability.
How does ABC classification work? (And what is wrong with it?)
To understand why ABC inventory classification falls short, let us unpack how it works. Traditional inventory management applications calculate safety stock for each individual Item-Location (warehouse) combination in isolation. For such an application to work, the planner needs to assign a service level target (%) for every combination.
With companies often managing tens or hundreds of thousands, or even millions, of Item-Location combinations, it is impractical to set service levels individually. A simplification is necessary, and ABC classification is one way of doing it.
A common approach is to use a 3×3 matrix with volume value on the Y-axis and order lines on the X-axis, creating a “double” ABC classification. Typically, 80% of the volume value is assigned to A items, 15% to B items, and 5% to C items. The same 80/15/5 breakdown applies to the number of order lines. A few high-volume value items usually hit the 80% threshold of the AA category quickly, leaving most items in the CC category.
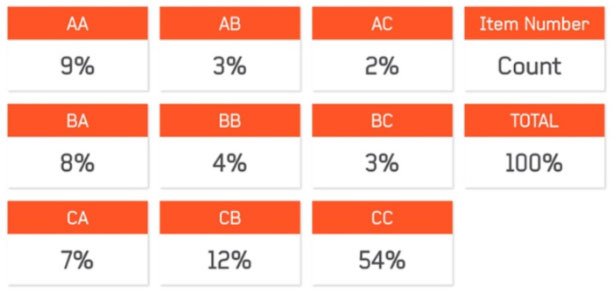
Service levels are then assigned to each ABC class through a “trial-and-error” process. The AA class typically gets the highest service level targets, and the CC class gets the lowest.
If the aggregated service level doesn’t meet the company’s overall target, say, 95.o%, adjustments are made to the service level targets per class. Once the settings are in line with, or slightly above, the company´s overall target, 95.5% in this example, the process stops.
Now every item in each ABC class shares the same service level target. For example, if there are 10,000 stocked items in a location, all 5,400 items (54% from the ABC classification example above) in the CC class will have the same target. Safety stock levels can then be calculated.
The drawbacks of ABC classification
Now, let us pause and think for a moment.
The stock investment depends on the service levels set for each ABC class. Could other service level combinations achieve the same 95.5% result? Absolutely. There are countless combinations that could give the same 95.5% overall service level, all with different stock investments.
So, how do we know if our chosen assignment of service level per ABC class is optimal? We don’t. That’s why we call it inventory management – not inventory optimization.
The example above describes one level, but supply chains are often more complex, with multiple levels/tiers (central, regional, and local warehouses). Some traditional inventory management software uses an 8×8 ABC matrix for each location. With many locations, setting up and maintaining this system can become a very labor-intensive task. And we still can’t be sure if we have the optimal set-up.
Why inventory optimization beats traditional inventory management
So, is there a better way to segment items, assign service level targets, and optimize safety stock levels today? Yes, there is.
While traditional ABC classification focuses on operational logistics, often ignoring sales, marketing, and customer needs, inventory optimization looks at the product range and the business.
This modern approach uses “Service Classes,“ for example, “Accessories”, “High-margin products”, “own-brands”, and “Critical spare parts”. This categorization is more relevant to sales and marketing, who might not even understand ABC classification.
Stock-to-service for better inventory management
In inventory optimization, you set service level targets per service class, not ABC class. The software optimizes each Item-Location’s service level and safety stock level using a “stock-to-service” curve. This ensures that you meet the aggregated service class target but with minimal stock investment. Let´s think about this. Using the ABC approach, all items in a class are assigned the same service level as an input. In inventory optimization, the software optimizes the individual Item-Location service level, this is an output,
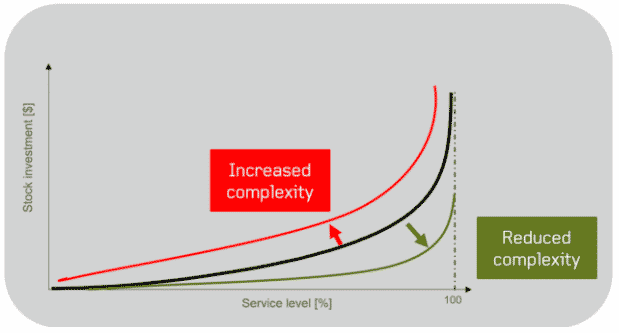
This automated differentiation of service levels (known as mix optimization) within each service class, considering lower bounds, is an outstanding way to reduce stock investment and increase service level at the same time. For example, “Accessories” might have an overall target of 93%, with a lower bound of 90%. The software then assigns service levels between 90% and 99.99% in such a way that the service class still reaches 93% as a group but with minimum stock investment, i.e. optimization. Similarly, “Critical spare parts” may target 99.5%, with a lower bound of 99.0%, still giving the system some level of freedom in the mix optimization step.
The result? Each item in each location is optimized individually but in relation to all other items in the same service class and in relation to upstream and downstream locations (known as Multi-Echelon Inventory Optimization, MEIO). Actually, they compete about the stock investment among each other you could say. In inventory management, items are treated as isolated entities. Inventory optimization software models tens of variables such as demand variability, standard cost, order quantity, lead time, lead time variability and more – unmanageable with the traditional approach.
Modern inventory optimization automates the planning of complex supply chains with hundreds of thousands of Item-Location combinations, guaranteeing service levels with minimum stock investment. This is all done with a very limited number of planners.
Ready to upgrade your inventory management?
Are you still relying on old inventory management methods? Transform your inventory strategy today with cutting-edge inventory optimization tools. Say goodbye to outdated ABC classification and hello to smart, efficient, and cost-effective inventory optimization.